World of OZ
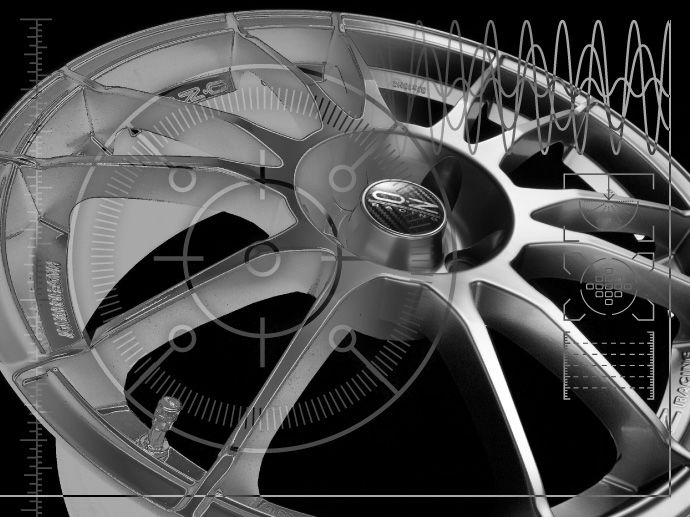
OZ Tech Lab
This is the nerve center of the company, where the most elegant technological solutions for product development and the manufacturing processes take shape daily. It’s where all the wheels that over the years have brought OZ its legendary fame were designed. Inside the OZ Tech Lab™ a team of engineers and designers is at work every day to develop exclusive, breakthrough technologies in a quest to find and test the most innovative materials, transferring all the know-how and experience acquired in more than 30 years of racing to its’ after market wheels.
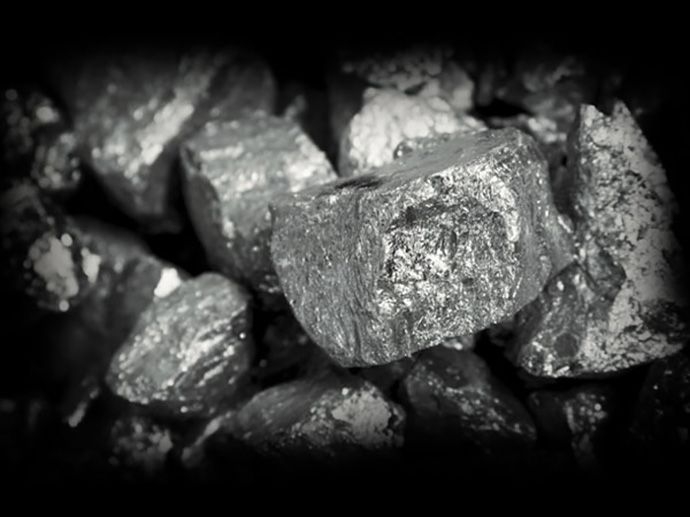
Raw Materials
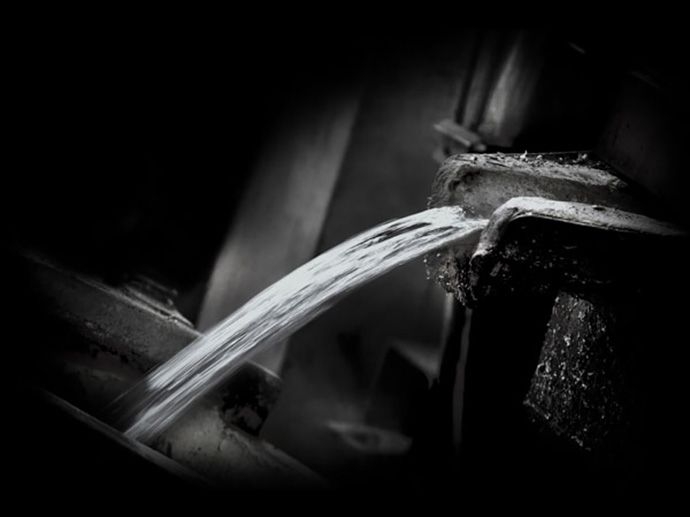
Casting
A quality starting from technology processes OZ wheels are produced through Low Pressure Casting and Gravity technologies. Low pressure casting the alloy is heated at about 700°C, cast and is low pressure injected into the bottom of the mould, to the top. This process is widely used to transform non-ferrous materials and alloys into manufactured products guaranteeing a high finishing level on the final product. The resulting casting won’t present any junctions, porosity or cavities and the raw manufactured wheel shall have a fine and compact grain.
The following alloy compounds are used in the manufacture of OZ wheels: G-AlSi7Mg.
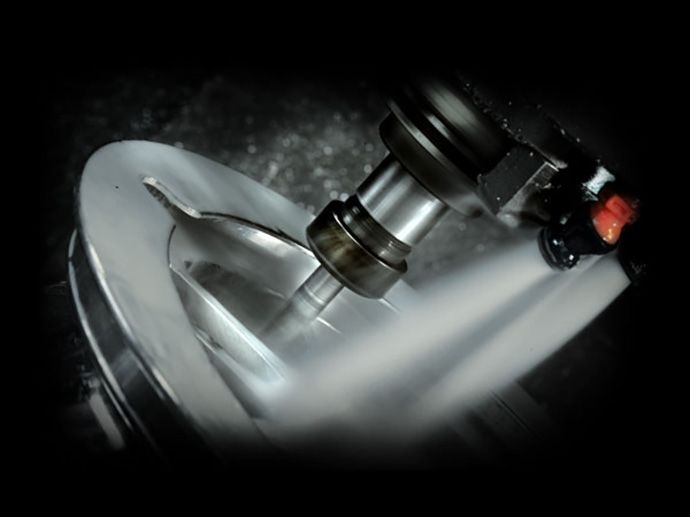
Forging
Forging: a great combination of strength, lightness and ductility.
The mechanical and physical strength characteristics of a forged wheel are equally distributed throughout the wheel on a molecular level. The result is far greater strength and resistance than an equivalent cast wheel, vastly improving the performance of the wheel when faced with impacts and high levels of load stress.
Read more
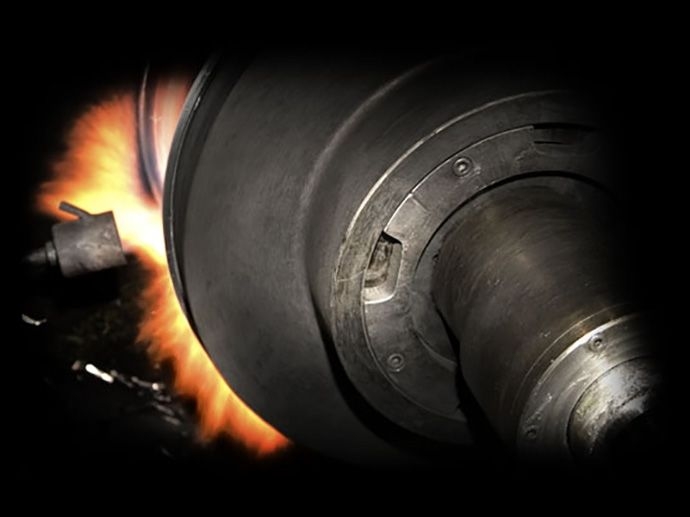
HLT
High Light Technology.
Manufacturing technology to improve lightweight characteristics to the wheel, with an even higher performance driving dynamics and a structural integrity to surpass the most stringent safety tests.
Read more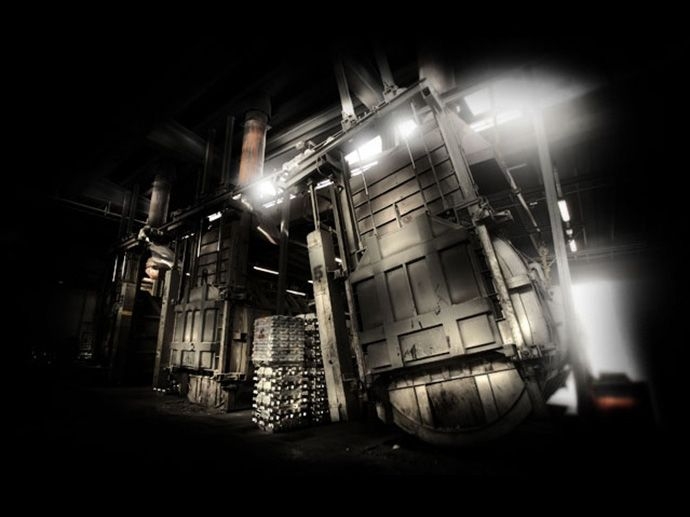
Machining and heat treatment
Machining and heat treatment are fundamental steps on the production process. From them we start shaping and giving strength to the wheel.
Read more
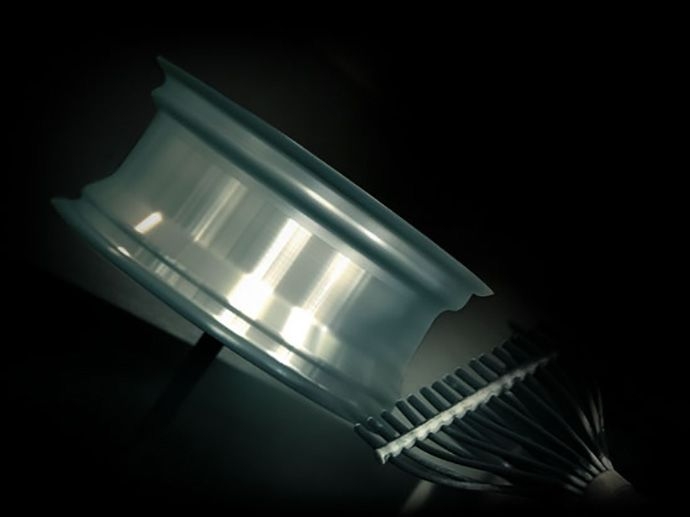
Finishing
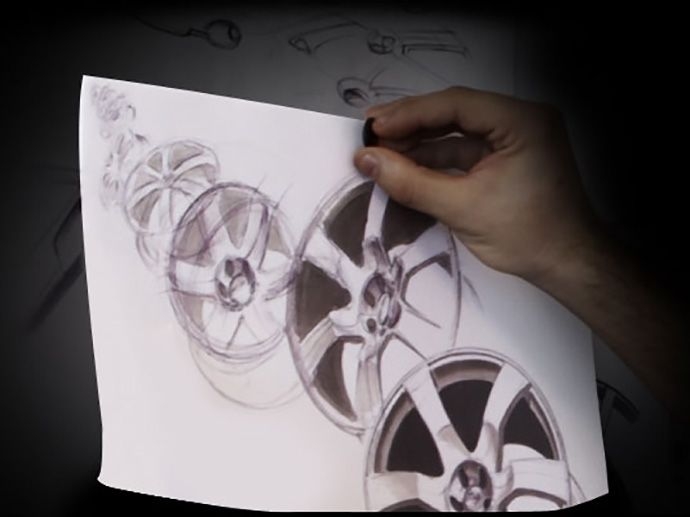
Concept
Creativity, innovation and technical experience: the OZ team’s successful formula.
The unique OZ style comes from an exchange of information between the OZ R&D Department and the best schools for designers in the world.
Read more
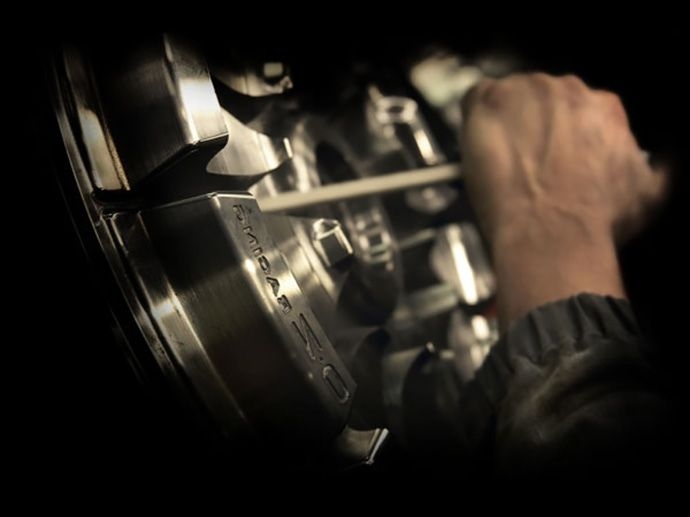
Development
From the idea to the computer technologies.
To support its designers, OZ adopts modern computerised analysis and design systems that improve production standards and drastically reduce time-to-market.
Read more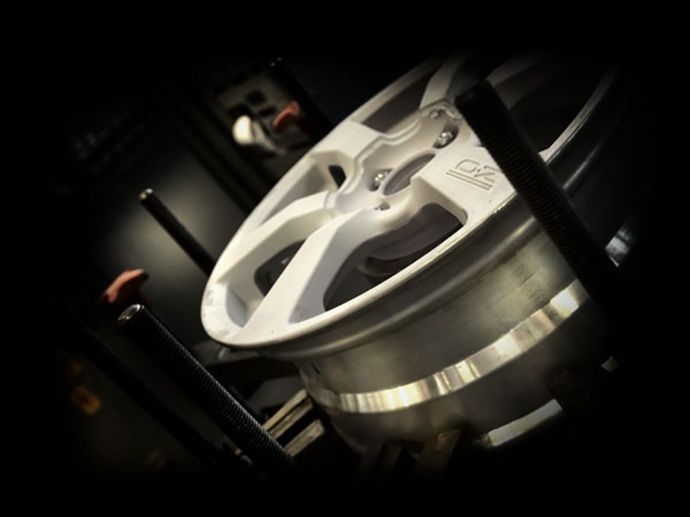
Pre-Series Test
A question of safety.
Pre-series wheels are tested according to the demanding standards of the German TÜV and of the Japanese JWL VIA Homologation Institutes.
All tests on the wheels are made at the internal testing facilities within the OZ manufacturing facility, fully equipped with the appropriate equipment for assessment certified by TÜV and JWL VIA Institutes.OZ is authorized by these Institutes to certify wheels itself.
All OZ products are TÜV certified. The most important tests required by TÜV and JWL VIA Institutes are the Rotary bending, Rolling, Impact, and Biaxial stress tests.
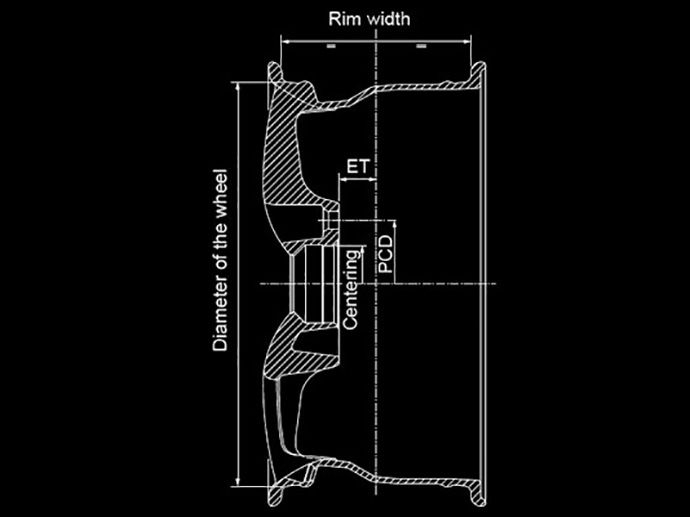
Measurement
- Diameter (inches): The diameter of the wheel
- Rim width (inches): The width of the part of the wheel where the tyre is fitted
- ET (mm): from the German “Einpresstiefe“ or “Offset” in English, it indicates the distance between the centre line of the rim wheel and the part of the wheel where the car's hub gets seated
- PCD (mm): from English “Pitch Circle Diameter”, it indicates the diameter of the circle that connects the centre of the fixing holes
- Hole Nr: The number of holes on the wheel necessary to fix it to the car. It appears together with the PCD
- Centering (mm): also called “Center Bore” (CB), it indicates the diameter of the center hole where the car's hub gets seated
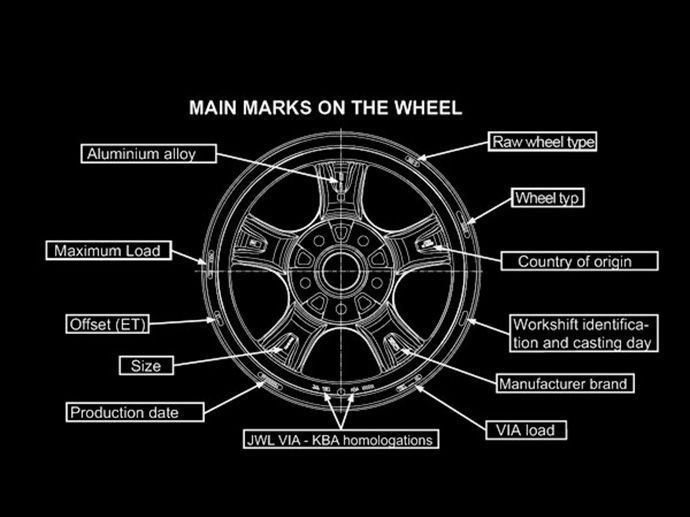
Marking
